Laser marking and Inkjet
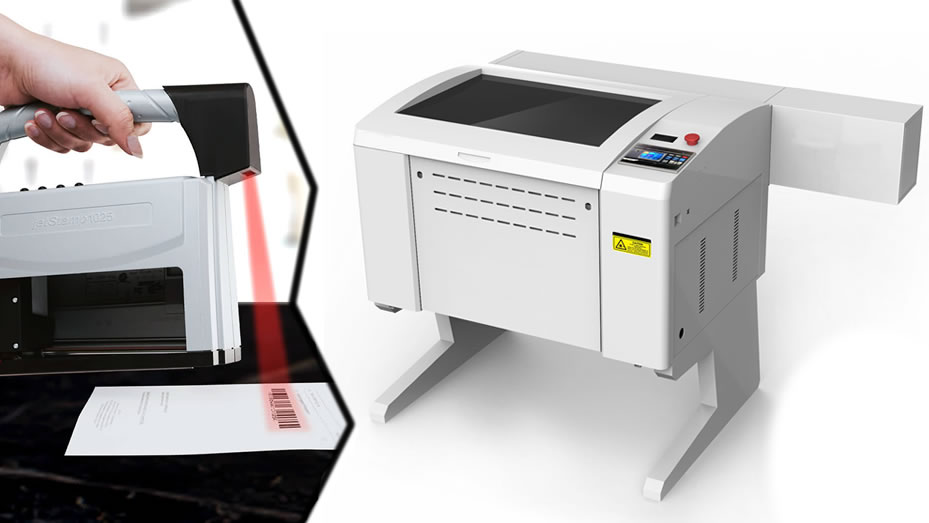
Laser marking is suitable for applications requiring precision, durability, and versatility across a wide range of materials, while inkjet marking is more suitable for applications on porous surfaces and for printing text and barcodes. The choice between the two depends on the specific requirements. Let's summarize the five main differences in a table.
Laser Marking | Inkjet Marking |
---|---|
Uses a high-energy laser beam to engrave or vaporize material on the surface. | Uses a printhead that sprays small drops of ink onto the surface to create the desired mark. |
More suitable for materials such as metals, plastics, glass, and ceramics. | More suitable for porous surfaces like paper, cardboard, wood, or absorbent plastics. |
Generally faster marking speed. | Requires time for ink placement and drying, so marking speed may be slower. |
Creates permanent, high-quality markings. | May require specific inks to ensure good adhesion and durability. |
Offers greater flexibility in design and material choice. | Better suited for printing text, barcodes, or simple graphics. |
Now let's explain them in a brief list:
1. Operating principle: Laser marking uses a high-energy laser beam to engrave or vaporize material on the surface. The laser creates a permanent mark by abrasion or material removal. On the other hand, inkjet marking uses a printhead that sprays small drops of ink onto the surface to create the desired mark.
2. Marking type: Laser markers are highly precise and detailed across a wide range of materials, including metals, plastics, glass, and ceramics. They can create fine lines, small characters, and machine-readable barcodes. Inkjet marking is more suitable for marking on porous surfaces like paper, cardboard, wood, or absorbent plastics.
3. Marking speed: Laser engravers are generally faster than inkjet marking. The laser can create high-speed markings without the need for direct contact with the material surface. Conversely, inkjet marking requires time for ink placement and drying, so marking speed may be slower.
4. Materials and durability: Laser marking is suitable for a wide range of materials, including metals, plastics, glass, wood, and many others. The laser process can create permanent, high-quality marks that withstand various environmental conditions, such as wear, corrosion, and exposure to chemicals. On the other hand, inkjet technology can be used on a variety of materials, but it may require specific inks to ensure good adhesion and durability.
5. Flexibility and versatility: Laser engraving offers greater flexibility in design and material choices, marking a wide range of shapes and sizes. It can also be used for marking on curved or irregular surfaces. Inkjet marking is better suited for applications where printing text, barcodes, or simple graphics is required.
Laser Marker Applications
Laser markers in CO2 and Fiber variants and inkjet markers are used in various industrial sectors. Here are some examples for both technologies:
• Marking and engraving metals to apply codes, serial numbers, logos, or traceability information on metal components.
• Marking plastic materials such as polymers, polystyrene, PVC, and many others. They are often used for product identification and branding on plastic products.
• Marking on glass and ceramics, for example, for applications in the automotive, furniture, or decorative object industries.
• Cutting and engraving fabrics and textiles, for example, for the production of clothing, carpets, curtains, or technical textile products.
Inkjet Marker Applications
Printing barcodes, text, expiration dates, or other information on food, pharmaceutical, and industrial product packaging.
• Labeling and printing on bottles, containers, jars, or other vessels, allowing for the quick and precise application of identification or branding information.
• Marking on porous materials like paper, cardboard, wood, textiles, or absorbent plastics used in the packaging, publishing, and woodworking industries.
• Marking on curved or irregular surfaces like pipes, metal profiles, or automotive parts, offering flexibility in marking objects of different shapes. These are just a few examples of applications, but both technologies have a wide range of uses across various industrial sectors depending on specific marking needs.